Redistributing global bending stiffness of corrugations with curved creases
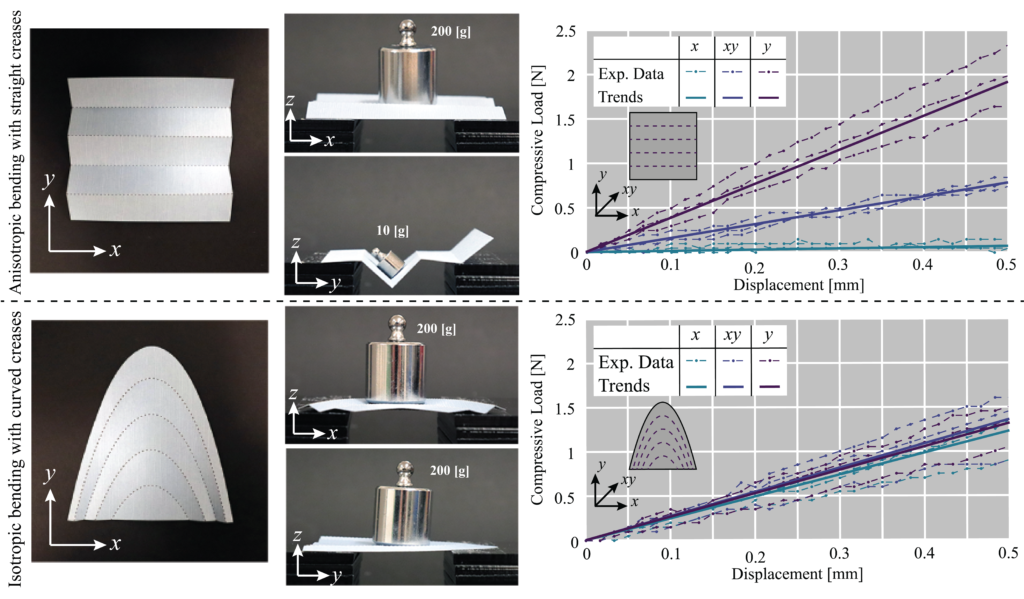
Corrugations are structures made from thin sheets that are folded in a repeated mountain and valley pattern. Because these structures are made from thin sheets, they are lightweight and save on material costs. Additionally, because material is displaced from the midsurface of the corrugation, these structures can resist bending deformations well. Indeed, a simple corrugation (like the one in the top-left of the figure above) is up to nearly 3,000 times stiffer than a flat sheet of material [1].
However, straight-crease corrugations are highly aniostropic. Depending on how the corrugation is supported, these corrugations might resist bending well or deflect too far. One solution that my research has explored is to use curved creases in corrugation designs. Because curved creases can change the direction of the crease, the weak direction of the fold changes throughout the structure. This results in a corrugation that distributes its weak points, resulting in a more isotropic bending behavior.
Because curved-crease origami starts from a flat sheet and does not require linerboards on the top and bottom of the corrugation, shipping and manufacturing of these corrugations are simplified. These corrugations are a great example of how curved-crease origami can be applied to practical engineering problems.
Related publications
Curved creases redistribute global bending stiffness in corrugations: theory and experimentation
References
[1] Gilewski, W., Pełczyński, J., & Stawarz, P. (2014). A Comparative Study of Origami Inspired Folded Plates. Procedia Engineering, 91, 220–225. https://doi.org/10.1016/j.proeng.2014.12.050